WBSP062: Grow Your Business by Continuously Monitoring the Emotional Response and Managing People Through Change w/ Amanda Prochaska
In this episode, we have our guest Amanda Prochaska, who discusses why managing people through change with large ERP transformation projects and continuous monitoring of emotional response is absolutely critical for the success of such projects. She also shares several stories related to emotional response and what she did to get these projects back on track and to bring positivity to the culture. Finally, she talks about what leaders need to do to identify the underlying symptoms of compliance culture and how to engage with vendors hired to help you manage this change.
Chapter Markers
- [0:16] Intro
- [2:54] Personal journey and current focus
- [5:29] Perspective on growth
- [6:55] The impact on the culture of an ERP implementation while managing people through change
- [14:04] Emotional response-driven ERP implementation
- [18:54] Why technology alone can’t help managing peple through change
- [20:35] Poor ERP adoption due to Compliance culture
- [27:04] How to build consensus and build trust in the ERP team?
- [28:01] Advice for leadership to work with external ERP consultants
- [32:22] Closing thoughts
- [33:52] Outro
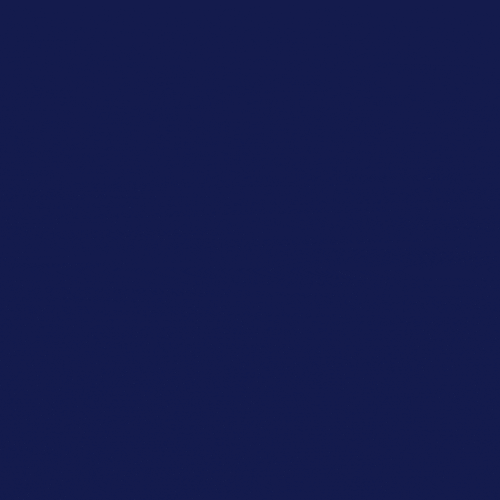
Key Takeaways
- Change, even in our personal lives, is hard. And there’s always an emotional response to it. So when I think about ERP implementations, these implementations are big and hairy. They touch all kinds of people in the organization. There are integration points that link people together. They’re not used to now all of a sudden. You’re sharing metrics, and you might have organizational changes that go on, in addition to just the technology one.
- So many times the ERP implementations fail while the technology works perfectly, and they have perfect process maps, and they saw through all of this. If they don’t focus on the people and the emotional responses, those people won’t get the results that they hoped and because of this issue, the adoption is likely to be poor.
- An engagement team is critical to make sure that we don’t ignore the emotional response within the organization and that we can hear that and respond to it effectively.
- When you talk about engagement when you do that, people feel heard, they feel appreciated, they feel understood. And then what they’ll do is they’ll start collaborating, they’ll start innovating, they’ll start leveraging the technology that you just deployed in different ways that you never even knew were possible because they were brought along with the change.
Subscribe and Review
Apple | Spotify | Stitcher | Google Podcasts | Deezer | Player FM | Castbox
About Amanda
An accomplished executive, Amanda Prochaska is known for her extensive leadership experience driving change, and her curiosity to always find ways to improve upon today’s standards. From MGM to Kraft Heinz to Kellogg to ConAgra – these companies are just a small sampling of her Fortune 500 16 year journey in procurement and supply chain.
She left corporate 2 years ago to become the Chief Wonder Officer at Wonder Services and the Chief Shimmer Officer at Global Women Procurement Professionals. Amanda’s motivation is to help your existing internal leadership increase your ROI through effective adoption of change and uplift women in procurement in their careers.
Resources
Full Transcript
Amanda Prochaska 0:00
While the technology works perfectly, and they have perfect process maps, and they sat through all of this, if they don’t focus on managing people through change and the emotional response of those people, they don’t get the results they want.
Intro 0:16
Growing a business requires a holistic approach that extends beyond sales and marketing. This approach needs alignment among people, processes, and technologies. So if you’re a business owner, operations, or finance leader looking to learn growth strategies from your peers and competitors, you’re tuned into the right podcast. Welcome to the WBS podcast, where scalable growth using business systems is our number one priority. Now, here is your host, Sam Gupta.
Sam Gupta 0:51
Yeah, everyone, welcome back to another episode of the WBS podcast. I’m Sam Gupta, your host, and principal consultant at a digital transformation consulting firm, ElevatIQ.
There is always so much at stake with ERP implementations. One plus one is perhaps 11 when it comes to deploying ERP. They are never just technology deployment. The companies that promise the world to their teams based on the overstated claims from technology sales professionals might encounter varied emotional responses from their leaders, leading to a compliance culture.
This culture often produces the exact opposite effect of what you intended to achieve with your technology. In today’s episode, we have our guest, Amanda Prochaska, who discusses how to prepare for change with large transformation projects and why a continuous monitoring of emotional response is absolutely critical for the success of such projects. She also shares several stories related to emotional response and what she did to get these projects back on track and to bring positivity to the culture. Finally, she talks about what leaders need to do to identify the underlying symptoms of compliance culture and how to engage with vendors to help you manage this stage.
Let me introduce Amanda to you.
Sam Gupta 2:00
An accomplished executive, Amanda Prochaska is known for her extensive leadership, experience driving change, and her curiosity to always find ways to improve upon today’s standards, from MGM to Kraft Heinz to Kellogg to Conagra. These companies are just a small sampling of our fortune 500, 16-year journey in procurement and supply chain. She left corporate two years ago to become the Chief Wonder Officer at Wonder Services and the Chief Shimmer Officer at Global Women Procurement Professionals. Amanda’s motivation is to help your existing internal leadership increase your ROI through effective adoption of change and uplift women in procurement in their careers.
With that, let’s get to the conversation.
Hey, welcome to the show. Amanda.
Amanda Prochaska 2:49
Thank you so much, Sam, for having me. This is amazing. I can’t wait to talk about the topic today.
Sam Gupta 2:54
And I’m so excited to talk about today’s topic because ERP implementations can have further implications. And typically, nobody sees this from the culture perspective. So I’m super, super excited to jump on that topic. But before we do that, do you want to kick things off with your personal story and current focus?
Amanda Prochaska 3:14
Oh, yeah, absolutely. So my personal story is one I like to describe as one of an adventure, a sense of wonder I’ve kind of meandered through my career. But what grounded me in my 16 years in procurement was leading large-scale transformation.
So I started out in my first journey right out of school was implementing a new travel agency program online booking tool, all the way through three SAP implementations, many Coupa implementations, whatever in the procurement space, I was typically leading those large digital transformations, but then I was opening properties, and doing M&A integration, which is a huge cultural impact. So what underpinned it all was this concept of change in how to lead change effectively, and really what works and what doesn’t work, because I’ve had plenty of failures along the way.
Sam Gupta 4:16
Yeah, we have not had anybody saying that they have not had the challenges during the implementation. If they otherwise, most likely, they are lying, right, Amanda?
Amanda Prochaska 4:23
Oh, absolutely. So what happened was my dream job at MGM, and I built a team from scratch. I was leading their best P2P transformation, having a ton of fun. And then I got the opportunity to go out on my own, and I’ve always wanted to be an entrepreneur, and this was about two and a half years ago, and really in the back of my head, I think I can help managing people through change through these initiatives, and not only get through them effectively but actually have a positive impact on the culture.
As an outcome, because I was the one thing that I felt was lacking was we would, we would tell people, hey, this is the technology change that’s going on. And people would just kind of take it in the chin. Instead of looking at this as okay, I have an opportunity not only to enable my organization with but also, let’s just say, a new technology, new ERP deployment. But let’s actually take the opportunity to build engagement, build an innovation culture. So that’s what I set out to do. And that’s the mission that I’m on right now.
Sam Gupta 5:29
That’s amazing. So obviously, it’s going to be a super, super exciting discussion, in my opinion. But before we do that, we have one of the standard questions that we ask all of our guests, and that is going to be Amanda. What is your perspective on growth? What does growth mean to you?
Amanda Prochaska 5:44
Oh, my gosh, it’s like the whole purpose, why we’re here on Earth? What it means, like, every single day, I was on a call, I was on a clubhouse room the other day, and they were talking about failing forward. And I was like, Oh, my gosh, I feel like I fail in little ways every single day. But I’m okay with that.
Because growth is all about reflecting on the world around you, watching what other people are doing, and saying what works and what doesn’t work. And really, every single engagement in my mind, like we’re just interacting here today and with your audience, is an opportunity to learn. So that’s really what it’s all about. And that’s what drives me every single day is growing.
And if I’m not growing, then I need to go do something else, right? And growth is not always fun, like going out and starting my own business. Oh my gosh, not fun at times. Like there’s been extreme highs, extreme lows, but I want to trade it for the world because I’m growing every single day. So I love this question.
Because we shouldn’t be afraid of growth, but we also know we can also realize that growth is hard at times, right? It’s not always sunshine and rainbows. It’s hard. Its blood, sweat, and tears, it’s energy that you have to put into it. But at the end of the day, it’s so worth it.
The impact on the culture of an ERP implementation while managing people through change
Sam Gupta 6:55
Yeah, and this is what I tell everybody. If anybody thinks that either growth is easy, or digital transformation is easy, or entrepreneurship is easy. They just don’t know what they’re talking about. So on that note, you are going to have tons and tons of stories around the impact on the culture due to ERP implementation.
So do you have any stories that you would like to share? The more you share, the more my audience is going to love it. We love stories around here, Amanda.
Amanda Prochaska 7:27
I love telling them to, so can I actually start with a non-ERP story? This is actually a personal thing that just happened to me this week. So I’ll start there because I think it sets the framework of what’s going on in a macro picture of ERP.
Amanda Prochaska 7:53
So, my daughter, she’s nine, okay. So last week, on Fridays, they don’t have school, we homeschool them. And so they have Fridays off. And she was really super excited that day because we were planning on taking her to the roller rink and perhaps a movie.
And she was going to do this with her sister. And she has all these plans in our head. And by eight o’clock in the morning, all of those plans changed, okay, they changed because her sister had to be across town at a dance competition. And we didn’t plan effectively. Let’s just use this put it that way.
So I literally crushed her dream. Like she came into my office and was sobbing. She was just totally distraught because she thought she was going to be doing one thing. And in a matter of minutes, it changed. And her reaction was to cry.
Amanda Prochaska 8:52
Other people’s reaction, like the one that I had later on in the week, was anger. Yeah, so I was invited to a webinar. And I was supposed to host a breakout session and that breakout session, so I was going to be on screen. So working from home, I had to put on makeup and do my hair and get all ready.
And I was highly prepared, really excited about the topic, like just really amped up to talk about this and lead a conversation of women through the topic. So we get to the point of the breakout room, and I get put in the wrong room. Oh, wow. And the other moderator in the room was like, Well, I’m moderating this room. I don’t know what’s yours.
And I was so mad because I thought I was going to be doing one thing. And now I’m not, and I did all of this preparation. I was super excited about it. And it just didn’t turn out the way that I had hoped I would remain, so when I wrote and I actually called a friend, and I said I am really mad about this right now and give me a perspective of how to manage this because it’s not right to be mad, but I am.
Amanda Prochaska 10:03
And I just need to work through it. And her advice was to call them back and ask for time, one on one, to do a webinar just with them about the topics that you were passionate about. So that’s what I did. And it worked out, we’re getting on a schedule, and it’s actually going to be better than I think what it was to it originally.
So I share these stories because change even in our personal lives, like when changes, plans change of expectations is hard. And there’s always an emotional response to it. And so when I think about ERP implementations, these implementations are big and hairy, right? They touch all kinds of people in the organization. There are integration points that link people together. They’re not used to now all of a sudden. You’re, you’re sharing metrics, and you might have organizational changes that go on, in addition to just the technology one.
Amanda Prochaska 10:57
And what I learned throughout my career is to never forget that emotional response. And that’s why I think so many times the ERP implementations fail while the technology works perfectly, and they have perfect process maps, and they saw through all of this if they don’t focus on managing people through change and the emotional responses, those people, they don’t get the results that they want that anymore. Right?
I saw a post that you made today, and it was you reflecting on people, processes, and technology for ERP implementations. And that to me, and we put managing people through change first for a reason. But sometimes, in the change management world, we start focusing on the technology and the technology changes. And when people want me to do when the system versus having an honest and open conversation about the emotional response that they might be having to that.
Sam Gupta 11:53
Yeah, so you started with the technology, then the most recent ones are going to be pretty bad. That’s what I can tell you.
Amanda Prochaska 11:59
Yeah. So I have a current situation going on. And it impacts the sales team. Okay. So they’re moving from a process where they’re getting today. They’re getting phone calls from their customers for orders. Yeah. And tomorrow, those orders are going to go through an e-commerce type of solution.
So very, very interesting. And the salespeople are really excited about the change, right? They’re like, Yay, finally ecommerce, right? But what’s the emotional response, though? Initially, we might be excited about something. But as we talked about, at the very beginning, exactly. Change is hard, right? Or whatever. If you’re growing, it’s hard. So initial response might be like, yeah, I’m starting my own company, and then you dive into it two days later, and you’re like, holy crap, it’s hard, right?
Amanda Prochaska 12:52
So that is like, the thing that we’re concentrating on with the salespeople is like, we don’t want to leave a void. We don’t want to leave that void of Okay. They’re no longer contacting their customers the way that they used to.
So what do we want them to do? Do we want them to proactively reach out to those customers and continue to build a different relationship with them? What are they going to do with their time? If they’re not answering phone calls? What are they going to do instead? How are they going to feel about compensation? Is there going to be any compensation impact on that? And how are they going to really feel about that and react to it?
And so even though they’re excited, yay, about e-commerce, you have to think through that response. And we don’t want to leave a void. And we don’t want to leave fears in people and acknowledge that they have those emotions, and then figure out how to approach it and make them understand the big picture.
And then the small picture, the micro picture of how it is impacting them. But at the end of the day, the conversation I wanted to have today around that cultural impact and how you can look at this as an amazing opportunity to engage your organization in a different way.
Emotional response-driven ERP implementation and its importance while managing people through change
Sam Gupta 14:04
Yep. So I’m a big fan of emotional response-driven ERP implementations, and I’m actually going to steal that phrase. Okay, so now, let’s talk about the emotional response-driven engagements that you have done. And in some cases, I can almost guarantee this, Amanda. When we get into the ERP implementation, there are going to be some very strong emotional responses in terms of anger.
So tell us some stories where either you did something because somebody got angry and they got angry for a reason. As you mentioned, we need to acknowledge that, right? So tell us any story you have where there was real anger, and then you had to manage that change through the process.
And finally, I mean, there was some sort of excitement because any change is going to bring some positivity to the culture. So tell us some stories where it was real anger, and you had to manage the situation. And then there was a positive change towards the end that they understood and appreciated it.
Amanda Prochaska 15:06
Yeah. So I actually have two stories in mind. So one of my pet peeves, one of my biggest pet peeves, are leaders who over-promised during these implementations, yeah. So you go out there. And as a leader, you want this to work, right? You want it to have a positive impact.
But there’s also this kind of line that you can craft around over-promising. So often, I’ll go into different companies, and they’re like, this is going to save world hunger. And this is going to, like, the tool itself, right? Like, it’s going to do all this stuff. And I’m like, let’s pull back that scenario and try to be authentic. The authentic story is, this is going to have benefits. And these are the benefits that we’re expecting.
Amanda Prochaska 15:53
But we also know that change is hard. And this is what you can expect on this journey. You can expect to have fears. You can expect to have those emotions. So that’s the case. I’m usually walking into where you have someone who hasn’t thought through that.
And then in these organizations, like one of my clients right now, where it leaves organizations not believing their leadership, right, you do that. And then the next change, they’re angry, because they didn’t see the tool saved world hunger, does start not believing what the leaders have to say.
And so the next change comes down. And what happens is, they just were like, tell me what to do. And I’ll do it. And it leads to this compliance culture, where I’m just now an order taker. And I’m not thinking through how I can innovate now because of this technology or this change. I’m not looking at how I can collaborate with other people.
I’m just waiting for leadership to tell me the next story that I’m not going to really believe anyway. And that’s what I call the compliance culture. Like that is not what you want. That’s the siloed that is the people who are just waiting for the next shoe to drop. And ultimately, you are never going to get the results from your ERP implementation.
If you have a culture like that. And that’s driven by fear that’s driven by anger. Yep. Right. That is where those and I feel for him. I’ve been there like I’ve done it to people. Sam, I remember somebody, one of my first implementations, large P2P implementation.
Sam Gupta 17:30
On that point, you are not the only one. We all have been there. Right.
Amanda Prochaska 17:37
And I reflect on it now. And Sam, I’m like, Oh, it’s so not the right thing to do. Yeah, it really wasn’t. But I think it was a lack of perspective, maybe. But I was implementing a P2P and promising that this was going to be a silver bullet. Everyone and never talked about what it takes to get there.
Yep. I just talked about the future state. And it led to post-implementation, what happened was you had people who were like, well, are we really getting the results that we wanted, and they just started questioning, oh, this is a lot harder than we like what you the picture that you painted, like, okay, and you don’t want that type of response.
You want to be transparent and open, and honest with people about how you bring them along on that change. So number one thing if we can avoid that compliance culture and avoid over-promising and avoid just telling people what they have to do, and expecting them to do it instead of understanding that emotional response change would have such a better impact on the overall ROI that is expected within that ERP deployment and then also have a positive impact on the overall engagement of the organization.
Why technology alone can’t help managing peple through change
Sam Gupta 18:54
Yeah, and I could not agree more with that story, and especially I’m super sensitive towards these buzzwords and these disruptive things, and as you know Amanda, I do a lot of podcasts here right, so I get a lot of it how their technology is so amazing. It’s going to change the world, and I’m like, Okay, get me the real story.
Be specific on how it is going to help me, or I’m gonna hang up on you. And that is the only time when I hang up on anyone as I find this slightly disrespectful. In my opinion, when you say that and you’re absolutely right that you know you are really claiming that you are going to change the world when you are actually not going to change the world. I can promise you that. It’s going to be really hard to do that, by the way.
Amanda Prochaska 19:40
Yeah, well, and especially so right now and of one of my engagements I’m actually like, the truth fair because they’re trying to select a technology, a P2P technology right now. And so they’re getting sold to all day long by the salespeople. So they listen to the salespeople, and then they come to me, and they’re like, what’s real? That’s a reality because it’s like the technology itself without any of the people or the process changes or the organizational changes, the policy changes. Without all of that happening, technology is not going to solve your problem.
And it’s like, Now guys, like, let’s, let’s think about this differently. And yes, we can take it, we can understand what the salesperson is coming from, and they have an incentive to sell that technology. But we have to have reality. And we have to know that this is much more than just technology deployment.
Poor ERP adoption due to Compliance culture
Sam Gupta 20:35
Yep. So I mean, let’s talk about compliance. So in my experience, I think 90% of the organizations are probably going to have a compliance culture. This goes back to the way we communicate, let’s say, the change or vision of the organization. The state of the majority of the lifestyle businesses, in my experience, especially when you look at the manufacturing and distribution landscape, it is the reality. So what can you do? What specific strategies that you could use to change that compliance culture in your experience.
Amanda Prochaska 21:10
We actually start maybe at a different spot than most people. And when you take a step back, and the first question that we ask organizations is, why are you doing that? And most of the time, Sam, just like you just said, most of the time, it’s 90% compliance culture.
Most of the time, the reaction that we get is everyone else is doing it. Why are you doing? Because everyone else is doing? And it’s like, no. What specific problems are you trying to solve in your organization? So we started there, we started by putting the technology aside, and what problems are you trying to solve for the organization. It’s not just the leaders that get to talk about what problems you are solving. We go out and actually ask the people who are doing work, what problems do you want, followed by this initiative? And more importantly, Sam, we also ask the question, What don’t you want to be changed?
Amanda Prochaska 22:07
Yeah, right. Because some people like I have one instance right now, where we interviewed this individual, he’s the managing of a very important team within the change initiative. And he actually said, I don’t want anything to change. That’s really important to know. Because if he doesn’t want anything to change, well, he’s like, number one resistor on my list of we need to, we need to have a conversation about why he doesn’t think anything needs change, is there fear there?
Is there a comfort level that he doesn’t want to move from? Is he a couple of years from retirement, and he just doesn’t want to live through it again? I don’t know, but we need to dive in there. So we start there. But then we also have a conversation with the leadership team about, okay, this might be one of many changes, or an ERP implementation, it could go on for many, many years. And there could be other things that are associated with that ERP implementation that needs to happen.
Amanda Prochaska 23:03
So you don’t want to have the situation where, hey, I’m doing an ERP implementation. But oh, by the way, to do that effectively, I need to deploy a new WMS. And I also need to change how I manage all of my master data. If you don’t, if just those three things alone, if you don’t connect all those dots for people, people will make their own stories, that’s an emotional response, they will make their own conclusions, they will make their own story, and then they will start sharing that with other people.
Amanda Prochaska 23:46
So rather be reactive and then have that collective story. So we spend a lot of time there. And that’s before the project, most of the time is before the project even kicks off, which people think about change management.
Like it sometimes happens during blueprinted design. So that’s how we position ourselves differently to from the get-go. But one more important thing that I would highly recommend everyone to do is build an engagement team. And what I mean by that is, across all levels of the organization, you need to understand who your influencers are whom people trust, and they may have led change in the past or maybe not, but they have the ear of people within the organization, you understand who those people are, again, at all levels of the organization because you need that particularly middle management because the people in middle management get there like the black hole of change.
Amanda Prochaska 24:40
Typically people have done a really good job at the leadership level and at the people who are doing the work level. But that middle management needs to be focused, so you identify who’s the influencer, who are advisors. They’re not the people that are out there, influencing others, but they have their ear to the heart of the culture. They have the ear to the heart of what, where people are emotionally responding.
And those people will return that information to you. So you know what’s going on. Right? Then you also have your typical people like, hey, these are the people that do the work, and they do a damn well, and we need to involve them. And here are the leaders that need to be involved because they’re going to help influence at a different level. So we build out that kind of well-rounded team. And then, we feed them different information throughout the process.
Amanda Prochaska 25:32
For instance, we’ll have talking points for certain people, will have formal presentations for other people, will have one on one casual conversations that were needed to help him within the organization. So that engagement team is so critical to make sure that we understand that emotional response within the organization and that we can hear that and respond to it effectively.
So that and when you do that, Sam, when I talk about engagement when you do that people feel heard, they feel appreciated, they feel understood. And then what they’ll do is they’ll start collaborating, they’ll start innovating, they’ll start leveraging the technology that you just deployed in different ways that you never even knew were possible because they were brought along with the change.
And that’s all underpinned by passion has to be authentic, right? That if you develop a story that connects all the dots, but it’s not believable, it’s not going to go over very well. So that is what I love to do day in and day out. And what I love to see from a leadership perspective, Sam is a lightbulb starting to go off when you have these conversations.
You’re like, oh, okay, so I need to have this collective story. And I need to have a better answer than everyone else is doing it, which is just fried me every single time. But that’s how you do it day in and day out.
How to build consensus and build trust while managing people through change?
Sam Gupta 27:04
Yep. So we are going to discuss the compliance culture from a different twist or perspective since I mean that you have been on many large engagements. Now you are a consultant or VP, you have done them with very large corporations, and you will have hired the consultant the vendors as well.
And let’s look at it from the retail leaders’ perspective. Let’s say if I’m the manufacturing executive, I am the manufacturing CFO, right? I have had people in my organization for the last 20 years. And as you mentioned, everybody has their own fears, everybody has their own aspirations, everybody is driven by something, and that is their personal bias.
And everybody has that. If somebody says that no personal biases don’t exist, and everybody’s going to move to the organization, the personal biases need to be aligned to the organizational goals to be able to get the maximum or optimum output from these people. But let’s say if I’m the manufacturing executive, I have had these people for the last 20 years, and obviously, I trust them.
Advice for leadership to work with external ERP consultants
Sam Gupta 28:01
And that’s the reason why they were with the organization for the last 20 years, all of a sudden. I’m hiring a consultant or a vendor when he or she is promising me the word that I’m actually going to change the organization.
So obviously, it is going to be very difficult for the consultant, right. And as a leader, for me, it is going to be very hard for me to trust this consultant, whether he or she is right, my people are right, and I’m even more confused now. Okay, and then what I’m going to do is most likely, what I’m going to do is I’m not going to listen to the consultant as you are, let’s say proposing the changes that.
Okay, I’m going to change the world, and then all of a sudden, you get into that hard phase, and things don’t work out. And then what happens is the vendor that you hire or the consultant that you hire, he or she becomes compliant, right? In the customer-vendor scenario, he or she is going to lose the deal, so then we are going to be compliant with people doing so obviously, because of that, you are not going to get the results. So in this scenario, what your advice for leadership is?
Amanda Prochaska 29:05
Oh my gosh, yes. So it happens all the time. So in my experience out, oh, a contrast to experience is actually so I was doing a system implementation. And actually, it was kind of an interesting situation. But I was coming in at kind of the end of it.
And there was a third-party consultant, a system integrator who was helping us out on the project, and they were at a state where they were just taking orders. I was told that we were supposed to configure the system this way, or I was told that we needed to do it this way.
And they weren’t offering a fresh perspective around. No, guys, this is really how you should do it. And don’t go down that road you need to turn left instead of right, but they were just reacting to what the client was asking them to do because I think they were more motivated by trying to keep every one column and keeping that relationship going into the next project, versus truly trying to make a positive impact on this particular project.
So it happens all the time. The reverse of that, you also don’t want to have a third party necessarily solely driving a boat, either, right? You don’t want them to be the captain.
Amanda Prochaska 30:21
So there has to be this nice balance of asking questions and iterating on things. So I’ll give the example of what we did at MGM because I thought it worked really well. When I was still in the practitioner space, we actually had a third party on-site for two years, helping us with our source or patron information.
And the way that we worked that relationship was that we had this really good banter of questioning, and I think questions have such a powerful impact when it comes to this type of relationship. They would question, I would question back, they would question again. And we would go round and round until we both felt comfortable with the solution that we were providing it.
Also, I would ask them, like, this is what I feel but what’s best practice, what could be the best thing that we could do, and then let’s think about why that couldn’t work for us. So that type of banter back and forth, I think, is very, very healthy. And it should be actually sought after in these types of relationships. Now, that’s something that I’ve learned through my engagements. Now, as I’m on the other side of the table, right?
Amanda Prochaska 31:29
I find myself as more of an advisor, like, I’ll get on calls and just ask questions. Have you thought about this? Have you thought about that? What are you going to do about this? How are people going to react to that?
And typically, when you do that type of line of questioning and an invite, but that advisor has the leaders all of a sudden start having those lightbulb moments, and they come up with a conclusion that they believe are best through that line of questioning, and I’ll continue to question if I don’t think it’s the right thing to do.
But that’s I think the way to get through that I feel like I’m never really telling them what to do. And let’s say you particularly asked me for my opinion, and that my role is more about hey, have you thought about this? Have you thought about that? Why would that happen? Or how would they react and I think that works very, very well.
Sam Gupta 32:22
Okay, amazing. Amanda, this was a powerful conversation. Do you have any last-minute closing thoughts, by any chance?
Amanda Prochaska 32:28
So I would say if you are a leader facing change, which so many leaders are, I know in the procurement space, the average length of a CTO term in the role is three years. So if you can only imagine if your CTO is changing every three years, the strategy’s changing whatever is going on in your organization is changing at least every three years.
So you are facing change day in and day out. So if you are one of those leaders, remember that people come first. There will be an emotional reaction, and you need to understand what that is so that you can be effective in your change that you can drive adoption and ROI.
But they can also have a positive legacy within your organization, and bring your organization together, and have that true engagement from your team. So that is my number one thing I can leave your audience with is that remember that the people really matter and understanding that emotional response is key.
Sam Gupta 33:31
Okay, amazing. And my personal takeaway from this conversation is going to be any transformation, irrespective of whether it is ERP or any other transformation, don’t lead with technology or solution. Lead with an emotional response. On that note, Amanda, I really want to thank you for your time. This was a very fun conversation and super insightful.
Amanda Prochaska 33:50
Thank you so much for the opportunity. Sam.
Sam Gupta 33:52
I cannot thank our guests enough for coming on the show for sharing their knowledge and journey. I always pick up learnings from our guests, and hopefully, you’ll learn something new today.
If you want to learn more about Amanda or to meet Alice and learn more about how to become a change warrior, head over to wonderservices.net. Links and more information will also be available in the show notes.
If anything in this podcast resonated with you and your business, you might want to check out the related episodes, including the interview with Carol Marzouk from Leadership ‘n Soul, who discusses how to uncover and correct lingering toxicity before it extends your business growth. Also, the interview with Erin Koss, CPA from Syte Consulting Group who brings a unique and fresh perspective on how to manage large transformation projects in an environment with unexpected disruptions.
Also, don’t forget to subscribe and spread the word among folks with a similar background. If you have any questions or comments about the show, please review and rate us on your favorite podcasting platform or DM me on any social channels. I’ll try my best to respond personally and make sure you get help. Thank you, and I hope to catch you on the next episode of the WBS podcast.
Outro 35:02
Thank you for listening to another episode of the WB s podcast. Be sure to subscribe on your favorite podcasting platform so you never miss an episode. For more information on growth strategies for SMBs using ERP and digital transformation, check out our community at wbs.rocks. We’ll see you next time.